Glass door display freezers play a crucial role in the retail industry, providing an attractive and convenient way to showcase frozen products. However, as frost accumulates on the evaporator coils, it can hinder the freezer's efficiency and affect its performance. To counter this, defrosting methods are employed to remove the built-up frost.
Manual Defrost:Manual defrost is a traditional method where the freezer is turned off, and the accumulated frost is manually removed using tools such as scrapers or hot water. While manual defrosting allows for thorough cleaning, it requires shutting down the freezer and manually monitoring the defrosting process. This method can be time-consuming and may result in temporary loss of product visibility.
Timed Defrost:Timed defrost is a common defrosting method used in glass door display freezers. It involves setting a specific time interval for the defrost cycle, typically every 6 to 12 hours. The freezer temporarily stops cooling, and the defrost heater melts the accumulated frost. Timed defrost is relatively simple and automatic, but it may not be as energy-efficient since it operates on a fixed schedule regardless of the actual frost accumulation.
Adaptive Defrost:Adaptive defrost, also known as demand defrost, is a more advanced defrosting method that adjusts based on the freezer's actual frost accumulation. It utilizes sensors or algorithms to monitor the frost buildup on the evaporator coils. When a certain level of frost is detected, the defrost cycle is initiated. Adaptive defrosting helps optimize energy efficiency by defrosting only when necessary, reducing the overall defrost cycles and minimizing unnecessary cooling interruptions.
Hot Gas Defrost:Hot gas defrost is a more efficient and rapid defrosting method employed in some glass door display freezers. In this method, a portion of the refrigerant is redirected to the evaporator coils, bypassing the expansion valve. The high-pressure gas heats the coils, melting the frost. Hot gas defrost is faster than other methods, allowing for minimal interruption to the cooling process. However, it requires additional components and may be more complex and costly to implement.
Reverse Cycle Defrost (Reverse Hot Gas Defrost):Reverse cycle defrost, also known as reverse hot gas defrost, is an innovative defrosting method that aims to improve energy efficiency. It utilizes a valve to reverse the refrigerant flow through the evaporator coils, causing them to heat up and melt the frost. This method takes advantage of the heat generated by the compressor, reducing the need for additional energy consumption during the defrost cycle. Reverse cycle defrost is relatively efficient and minimizes downtime, making it a popular choice for many glass door display freezers.
Defrosting is an essential process in glass door display freezers to maintain their efficiency and ensure proper product visibility. By understanding different defrosting methods and their impact on efficiency, retailers can make informed decisions to optimize the performance of their display freezers. Whether employing traditional manual defrosting, timed defrost, adaptive defrost, hot gas defrost, or reverse cycle defrost, each method has its own advantages and considerations. Choosing the most suitable defrosting method depends on factors such as energy efficiency goals, equipment capabilities, and the specific needs of the retail environment. By implementing effective defrosting methods, retailers can enhance the longevity, performance, and overall efficiency of their glass door display freezers.
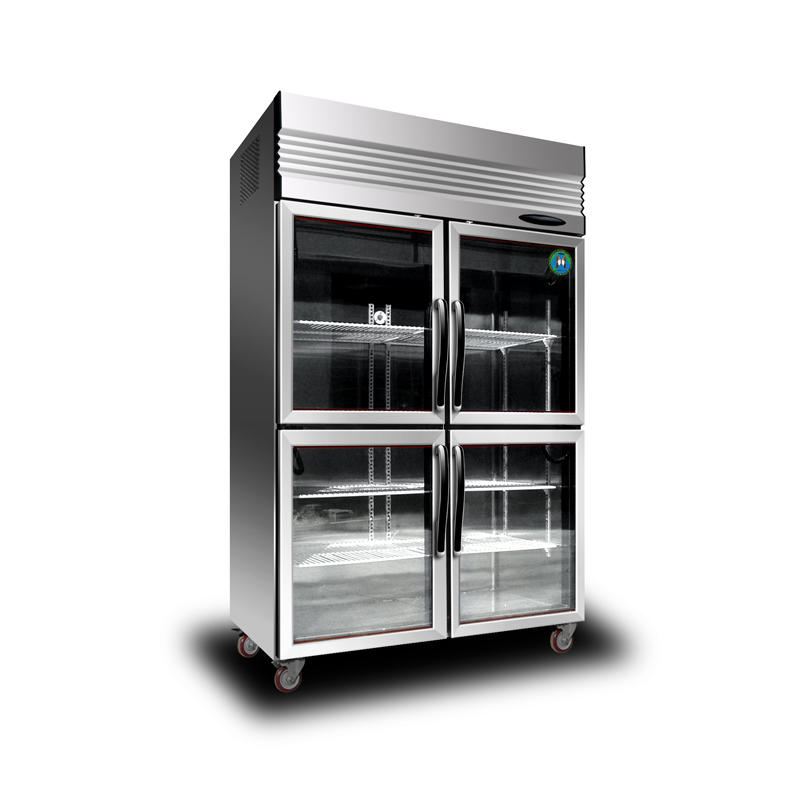
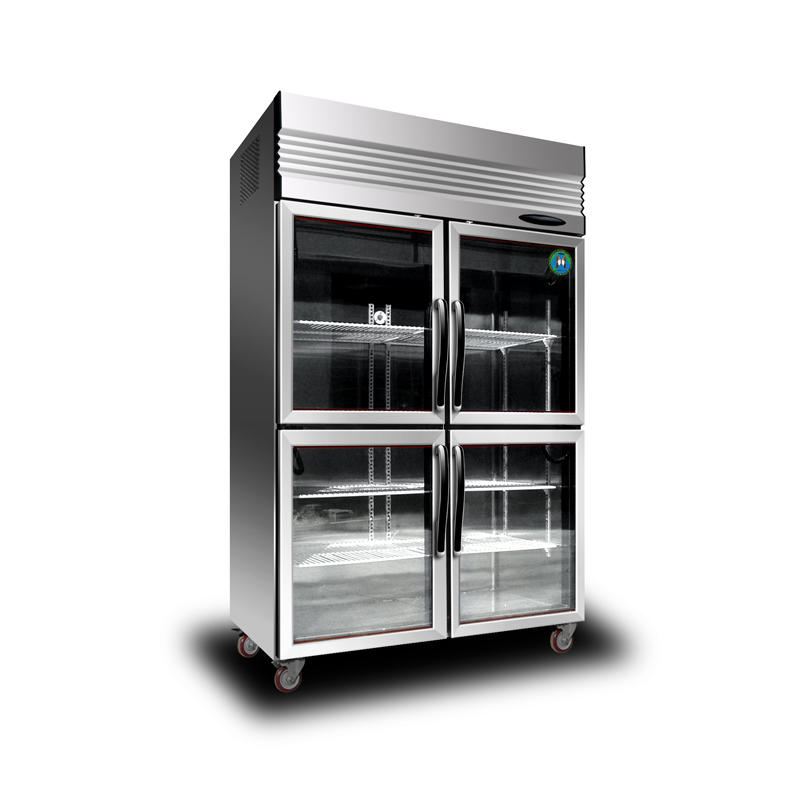
Model: RE-1200C / RE-1200F
Temp. range: +2~+12℃ / -18℃
Refrigerant: R134a / R404A
Voltage: 220V / 110V
Capacity: 900 liter
Dimension: 1200×760×1935mm
◎ Joint-in cooling unit, easy to maintain and mend.
◎ Big unit for high AMB and high humidity.
◎ 201 stainless steel inner and outer.
◎ Castors or adjustable feet.
◎ Digital temperature controller
◎ Heated glass, auto close door.
◎ Hydrophilic aluminum foil, internal thread copper tube.